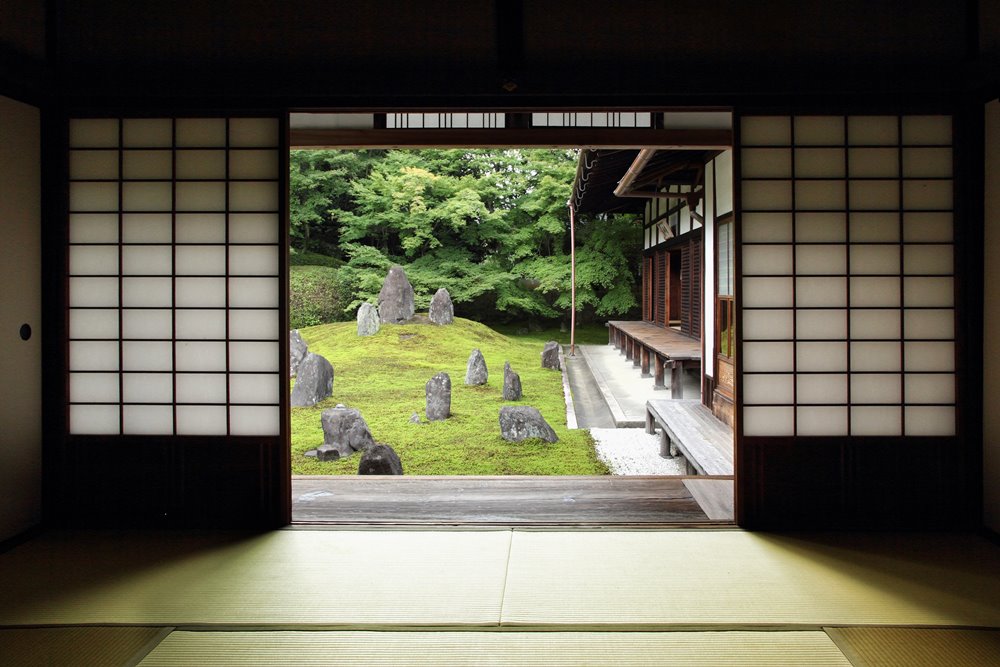
Wabi-Sabi
The Natural Beauty of Japanese Tableware
Japanese aesthetics, born from the spirit of "mono no aware" as seen in The Tale of Genji, and
intertwined with concepts like "yugen" (subtle profundity) and "wabi-sabi" (beauty in
imperfection), is deeply embedded in their tableware.
This beauty manifests in the way these vessels retain the marks of the maker’s hand, embracing
simplicity and avoiding unnecessary adornment. Even when worn or imperfect, these items are
cherished for their unique appeal. The asymmetry of Japanese ceramics is a direct expression of this
"natural beauty," preserving the raw textures and simple, organic patterns that embody an
unpretentious harmony.
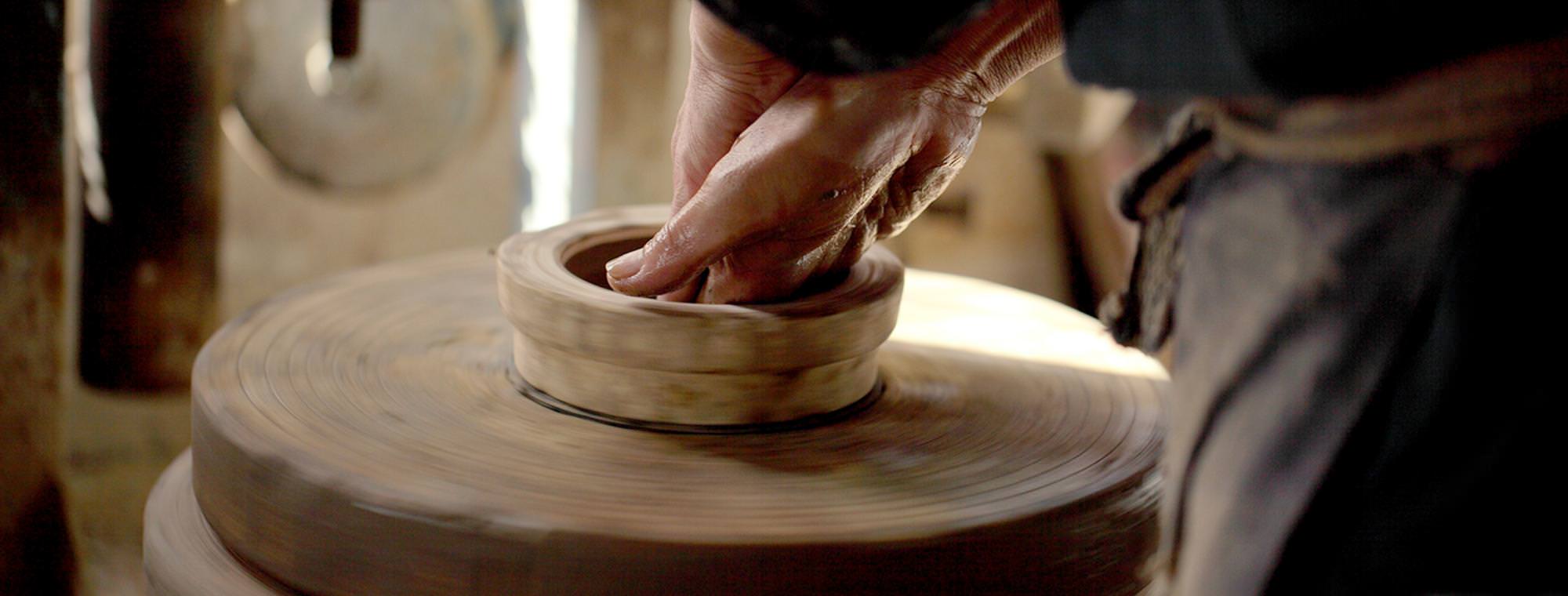
Ceramics
The fractures, wear, and stains that develop on these ceramics through daily use form a connection
between the user and the vessel, imbuing it with a life-affirming natural beauty. Even when
repaired, the imperfections are preserved as part of the object’s narrative.
Across Japan’s 47 prefectures, each region produces distinct ceramic wares, often named after their
place of origin, such as "Imari-yaki," "Karatsu-yaki," and "Mino-yaki."
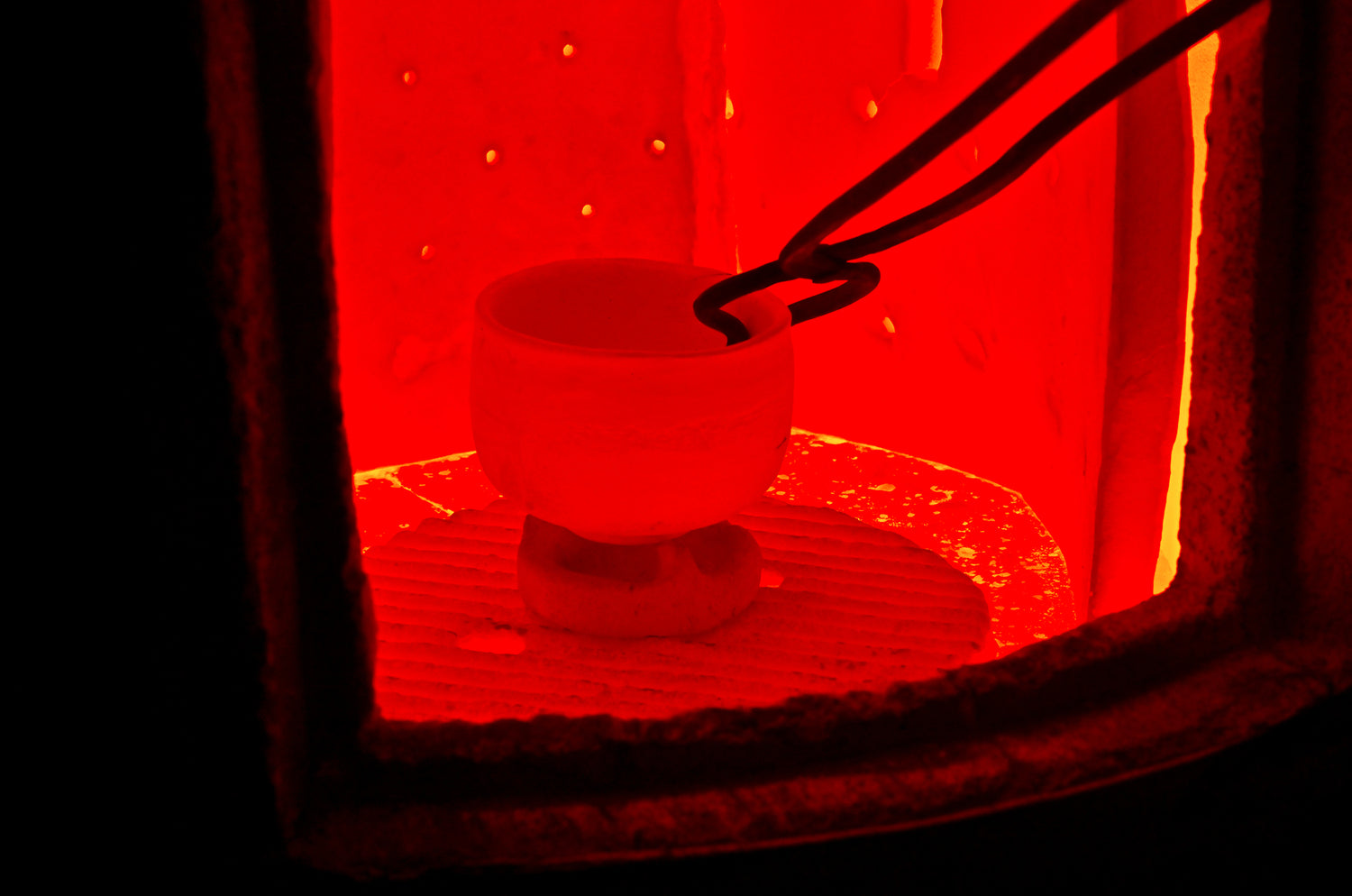
Kiyomizu-yaki
Named after Kyoto’s ancient Kiyomizu Temple, is renowned as a representative of
"Kyo-yaki." This form of pottery, perfected by Nonomura Ninsei in the mid-17th century, is
celebrated for its delicate painting and vibrant glazes. The intricate designs and varied techniques
make Kiyomizu-yaki a national treasure of Japan.
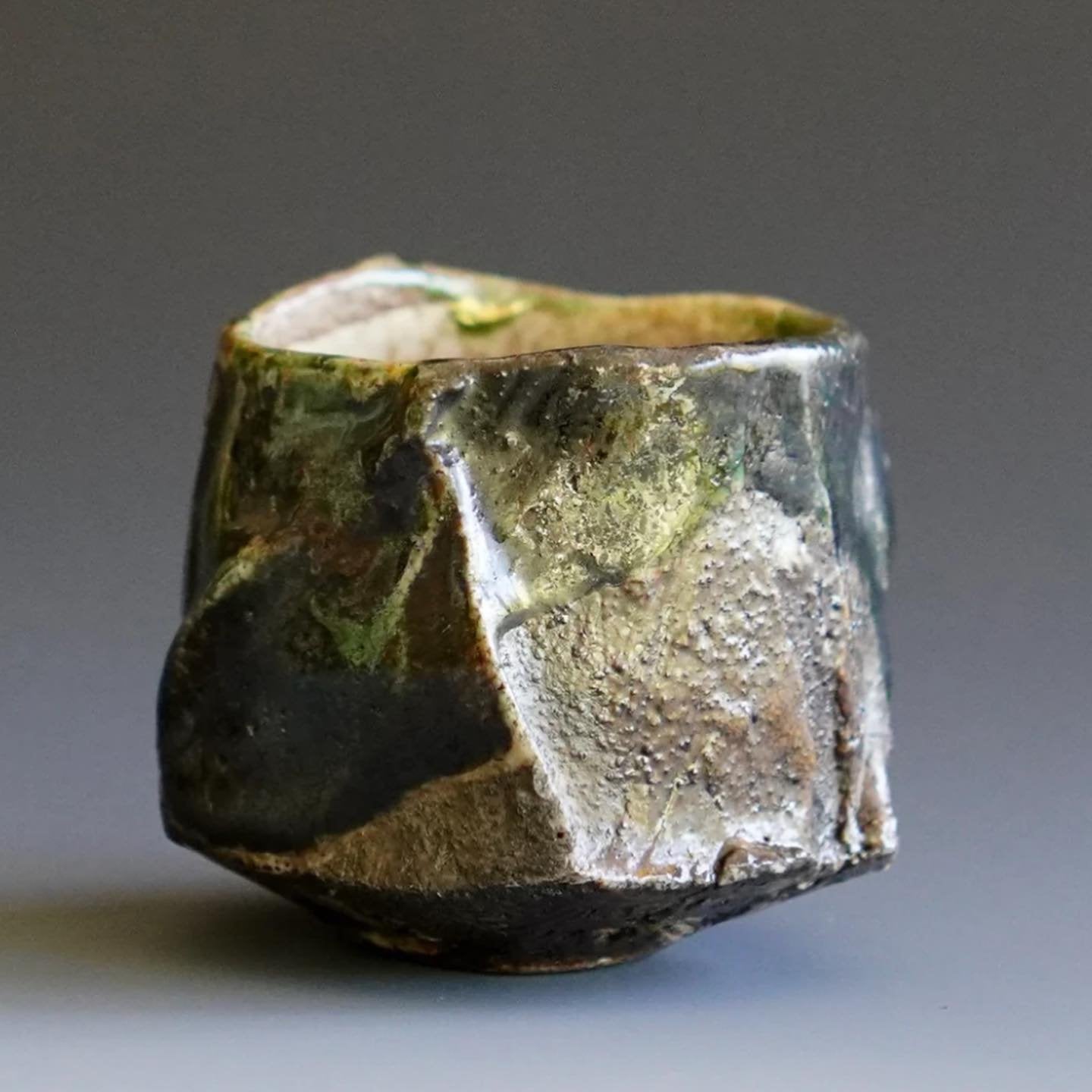
Mino-yaki
with a 1300-year history from the Tono region of Gifu Prefecture, is known for its
vibrant underglaze decoration. Fired at high temperatures of 1200-1300°C, the glazes fuse with the
clay body, producing a glossy, luminous surface. The irregularities in thickness, curvature, and form
give Mino-yaki its distinctive asymmetrical beauty, capturing the essence of freedom in
imperfection
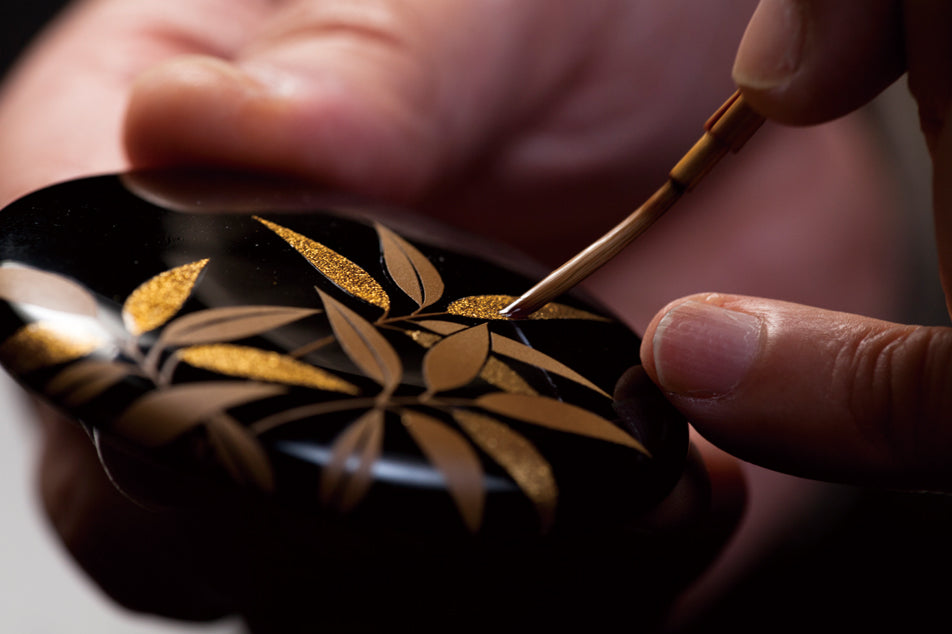
Lacquerware
Lacquerware, a unique craft of the East, flourished in countries like Japan, China, Korea, and
Southeast Asia. Among them, Japanese lacquerware gained global fame early on, so much so that
"Japan" became synonymous with lacquerware.For Japan, lacquer is a familiar and significant presence, with its use tracing back over 2,500 years
to the Jomon period. Lacquerware has woven itself into the fabric of Japanese life, serving as both
functional tableware and as decorative elements in architecture. Two representative decorative
techniques that have survived to this day are raden and maki-e.

Raden
Involves embedding thin, iridescent slices of shell, such as abalone or pearl oyster, into the
lacquer layers, creating luminous designs. The plum blossoms in the image below showcase this
technique, their vibrant hues crafted with intricate precision.
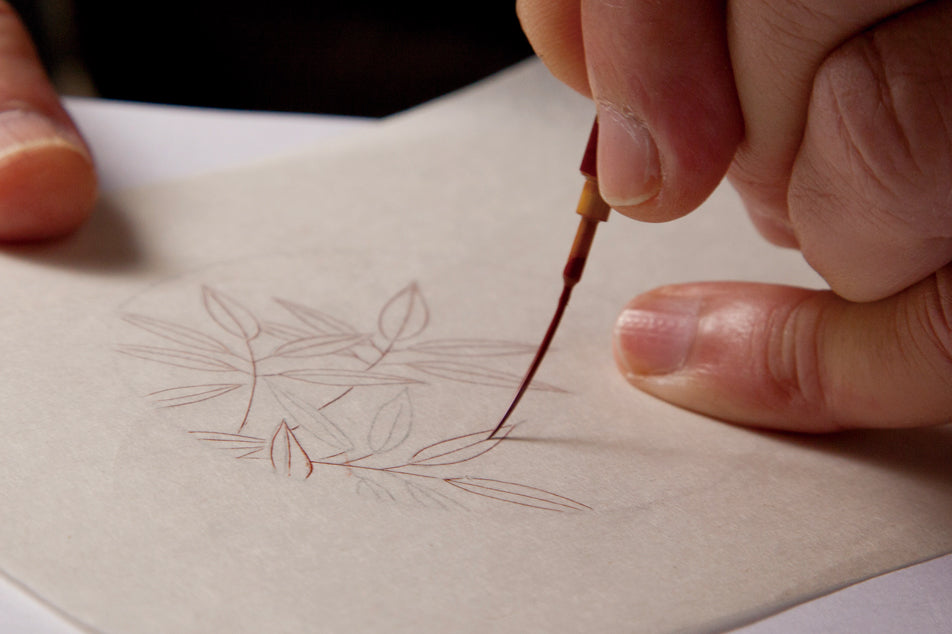
Maki-e
Is a technique where delicate patterns are drawn on the lacquer surface and embellished
with gold, silver, or other colors. The term "maki" originally referred to the sprinkling of gold or
silver powder, but today it also includes methods like inlaying metal foils. The lacquerware in the
above image, a fine example of Kanazawa lacquerware, is adorned primarily with maki-e, except
for the raden details.

Ochi-me
The outline pattern used in maki-e, is traced onto the thin Mino paper template, and then
lacquer is applied from the reverse side. The design is transferred onto the surface of the object,
dusted with a shell-based pigment called gofun, making the outline visible. Typically, these outlines
remain unseen by the observer.
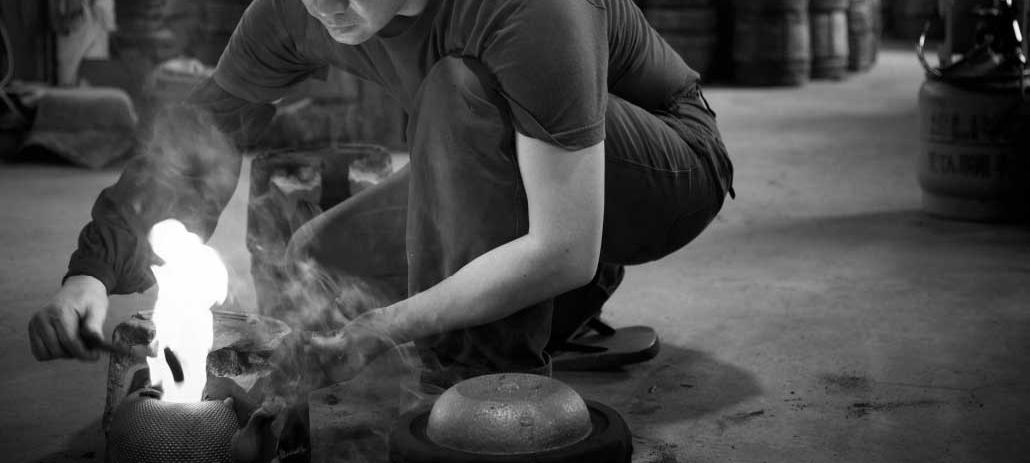
Ironware
Nambu ironware refers to the cast iron craftsmanship originating from the cities of Morioka and
Oshu in Japan’s Iwate Prefecture. These ironworks, known as Nambu ironware, are crafted from
natural iron, embodying a cycle of creation and return to nature. As household items, Nambu
ironware has been preserved for over 400 years, growing richer in texture and character with use,
each piece developing a unique patina influenced by its owner.
The most famous of these is the Nambu iron kettle, used for brewing tea. These kettles come in
various shapes, such as round, flat-bottomed ovals, and the natsume-maru, with traditional motifs
like cherry blossoms, chrysanthemums, peonies, pines, and auspicious animals such as horses and
turtles adorning their surfaces. Each kettle undergoes approximately 65 steps in its creation, most of
which are completed by hand. Becoming a craftsman takes at least 15 years, with each believing
that they must create with a user in mind, a belief passed down over 400 years.
The intricate process of making Nambu ironware begins with sketching the design, followed by
mold making, creating the clay mold, and then firing it. The molten iron is poured into the mold,
and once the basic form is achieved, the kettle is heated to 800-1000°C using charcoal to create a
protective film on its surface to prevent rusting. The entire process, with all its meticulous details,
can take nearly two months to complete a single piece.